When the heap cases are created for superposition, the recently introduced pressure and bowing examinations might be performed to gauge the pressure in the help column, σ, the avoidance because of pressure, oppression; and the redirection because of bowing, bending. The avoidance across the outside of the mold hole can be assessed as an element of the distance, x, from the centerline of the help column. Where L is the length of the range from the help column to the ejector rail and the scope of x is confined to one a large portion of the length of the range.
The greatest avoidance of the mold will happen either at the focal point of the help column or somewhere between the help column and the ejector rail, contingent upon the general sizes of the redirections. This prompts the accompanying equation for the most extreme avoidance given the superimposed pressure and twisting.
The mold creator ought to consistently consider the conveyance of the powers applied by the polymer liquefy in the cavity to decide the area and size of the help columns. Consistently dispersed help columns might be adequate, yet are once in a while ideal, Often, it is valuable for high-precision mould manufactory to break down the mold into discrete regions for primary investigation and plan.
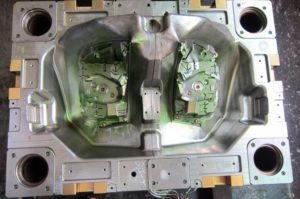
The underlying conduct of every 50% of the mold for eight depressions could be examined with a range of 359 mm and a width of 178 mm. The foundational layout may incorporate two huge help columns under each gathering of four cavities as appeared at left, or six more modest help columns separated between sets of depressions as appeared at right. The mold fashioner could likewise consider one help column straightforwardly under every pit. Every one of these plans can be examined. The last plan will be resolved by the underlying exhibition, yet in addition the discharge and upkeep contemplation. Once more, the easiest and most conservative plan is generally liked.
The mold format plan of oem injection mold factory is remarkable for two different reasons. In the first place, this plan shows 16 center additions pressed straightforwardly in a 4×4 matrix in one enormous pocket in the center plate with no interceding mold steel. This plan is substantially more smaller and less expensive to deliver than a plan with 16 individual pockets for the center supplements. Be that as it may, the plan will require cautious machining, completing, and get together of the mold embeds since resilience issues can cause positional mistakes and issues during trim, for example, coolant spills, blazing at the splitting line, or out of resistance molded parts. Second, the plan of china precision molds factory is a family mold in which each set of eight holes is molded with various thicknesses and at various liquefy pressures. Planning the hot sprinter feed framework would be testing. A stacked “X” type complex like the plan of plastic injection molding services china could be utilized with various measurements for the essential sprinters to adjust the dissolve pressures during filling.
Be that as it may, given the distinctive part thicknesses and comparative pressing weights gave to all the holes, the mold originator ought to anticipate less shrinkage in the more slender top moldings and specified a lower shrinkage esteem as needs be.
The portrayed investigation techniques give sensible direction to mold plan. On the other hand, primary recreations of injection mould manufacturers utilizing limited component investigation can be performed utilizing the point by point mold math. Such primary examination procedures are getting progressively coordinated with PC stream recreations to give high-devotion forecasts while likewise decreasing huge hindrances to routine usage.
This article is from https://www.injectionmouldchina.com