Basically, the injection molding process has been used the traditional way, which is known as the cold runner system. Nowadays, another method is getting popular. It’s known as the hot runner system. In this process, liquid substrate is put into the mold via a nozzle. So, the runner is kind of a passage through which the material travels. During the process, the substrate doesn’t cool down or get hard. Let’s find out why most people go for the hot runner for their plastic injection molds.
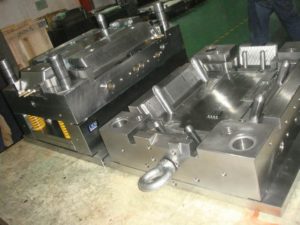
During a hot runner process, the mold is heated up and then cooled down once all of the cavity is full. Remember: the hot runner process may use many ways to heat up the injection mold, such as hot oil, hot water, induction/steam heating for quick heating. Unlike the cold runner system, this system cause fewer issues.
Now, let’s discuss why people go for the hot runner system in the injection molding process.
Less waste: This is an important point. In the hot runner system, the substance that passes through the chambers remains hot even when it reaches the last stage. In the cold molding, on the other hand, the runner is either discarded (waste) or recycled/reground. This is a disadvantage.
Quick cycle: As said earlier, the runner process requires time and may cause a loss of resource if enough time is not given. By fixing these problems, the hot runner system can boost the cycle times.
Keep in mind that the cooling and heating mold takes more time. Often, the time is offset through the savings from the elimination of the runner. However, it’s better to discuss the topic with your service provider.
Quality output: the removal of runners from the cold molded components requires a mechanical process. The product may get rejected if it is not up to the mark. In other words, the look and function of the product should be acceptable.
On the other hand, the hot molding can help resolve many issues, such as surface irregularities and burn marks, just to name a few.
Lower costs: cost is an importance consideration when opting for a cold or hot molding for a long-term. The initial cost of cold molding is less but the hot the hot runner system is a cost effective option as far as the long-term use is concerned.
Range of material: Actually, the inherent chemical composition of most of injection molding substance makes them a bit too “allergic” to temperature changes. The impact is stronger in extreme temperatures. So, for lower temperatures, the hot runner system is the way to go.
Colorant options: The hot runner system allows you to benefit from colorant mixtures in the process. So, this is another reason people opt for the hot runner process.
Long story short, these are the reasons the hot runner is an ideal choice for the majority of plastic injection mold projects. If you are looking to increase production in an efficient manner, we suggest that you give a go to this process. Hope this helps.
When it comes to hot runner injection mold, china plastic injection molding is the best choice.
Resource box: This article is originally posted in https://www.injectionmouldchina.com.