The plastic injection molding process in China is possible because any thermoplastic material can be melted to a predetermined size and the Injection molding machinery is designed such that it can then be injected into a mold or cavity where it can be formed. The parts of the mold which are in the shape of the parts to be manufactured are the cavities. The formed part is then ejected from the injection mold.
The sprue is a part of the runner which injects molten liquid plastic material into the die or Chinese mold through the injection machine’s nozzle. The runner system, as well as the sprue, is the passage that connects the nozzle of the machine to the mold cavities. Runner connects the sprue with the cavity through the gate. The nozzle of the machine is connected to the runner by the sprue and come in designs of hot sprue or cold sprue.
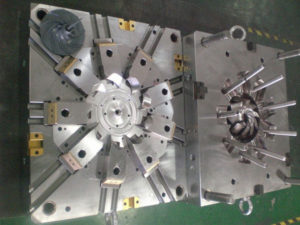
The Injection molding runner design comes in three basic types – hot runner, insulated runner, and cold runner. The runner has to ensure that the liquid material is distributed so that it fills all the China molds under the same conditions and the same pressure at the same time. This will help to prevent flashing of the china injection mold and also helps in producing parts of a uniform and improved quality. Hot runner technology, which is externally heated is more practical and feasible since the plastic is maintained in a liquid state and most China mold makers use this technology.
The usage of hot runners in injection molding machinery is useful since it ensures better quality parts. They are particularly beneficial with uneven-shaped parts which might result in improper cooling or uneven flow. Hot runners also help in reducing plastic wastage. They are designed to reduce cycle time, thus helping to maximize manufacturing productivity. The challenge in design is to maintain the liquid plastic which is molten at an optimum temperature while the china injection mold cavity is being cooled at the same time. Internal as well as external heating methods are used generally in injection molding machinery. Thus the hot runner technology, which was introduced almost 50 years before in the plastic industry, has revolutionized the china plastic injection molding technology and its processing capabilities by enhancing the efficiency of operation, improving the quality of the parts, reducing wastage and scrap and thus in effect saving money.
A very critical consideration for injection molding runner design as well as the china injection molding process is to maintain a uniform temperature in the hot-runner manifold and the sprue bar so as to ensure consistency in quality. Another consideration to be taken by China mold manufacturers is regarding the runner system. The injection mold china cavities will not be filled properly if the runner is too small. If the runner is too large, then cooling time will be increased and the cycle time will be decreased. Proper design for runners for injection molding china is most essential to reduce the effect of sink, stress, and weld marks.
A good and efficient runner design is most essential for plastic injection molding machinery as it helps in producing better quality parts at a very reasonable and affordable rate due to higher efficiency and lower wastage. Currently there are many suppliers who provide injection molding systems from China at very good quality.
Resource box: This article is originally posted in https://www.injectionmouldchina.com.