Gates and runners
An injection feeding model of injection molding china consists of various parts including the sprue which connects to the runner. The runner connects to the gate which is the smallest part in the radius, and then the gate finally joins the cavity of the mold. The proper gate and runner calculation of these parts are very important to keep the friction where the shear rate low. Balancing the pressure and temperature for proper flow of the plastic or resin is also essential.
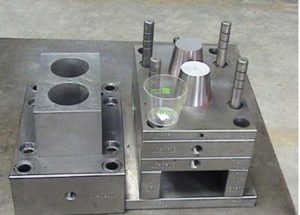
Calculating the runner size
The runner is part of the injection molding unit of a plastic mold manufacturers factory which connects the sprue and the gate. It is a cavity-like portion which holds the liquid plastic before it passes through the gate and fills the mold in the right way. Therefore, the size of the runner must be calibrated and optimized by all means. This is because a proper sized runner will keep the balance of the flow properly and the pressure will be optimized. The pressure plays a very important role to fill the mold and the runner. To keep a balance of the pressure among the two cavities, the runner pressure should be 25 percent or less of the total pressure to fill the mold. A good runner from injection mold maker china will also make sure that the fluid is heated to reduce the excessive pressure push.
Calculating and determining the right size of a runner is very crucial for plastic tooling china industry. Because it will determine whether the mold is filled properly or not. There are two major points to keep in mind. These are the thickness of the runner and morphology of the material to be passed. For Semi-crystalline materials, smaller runners are workable in injection molding tooling china. But there is a need for larger runners to facilitate temperature rise and reduction of pressure for the amorphous materials.
Calculating the gate size
Gate size is important for filling the part cavity properly since it is the section between the cavity and the runner. Proper pressure is important, which will determine whether the cavity will be filled uniformly or not. The two important things in injection mold tooling china about choosing the right gate size are to minimize the pressure drop and to have balanced control over the packing stage of the gate. There is a different type of gates that can be found in the double color mold parts like a ring, edge, pinpoint, disk and submarine. You have to keep in mind their sizes as well.
Larger gates corresponds to lower pressure increase. Packing stage is longer in this case and vice versa for the smaller gates. The gate is the place where the molten plastic goes through the shearing and has the most shear rate due to smaller cross-section area. Shear rate is influenced by the cross-sectional radius and flow of the material. It is crucial in china mold-building services to keep the shear lower while filling the gate to cause smaller injection damage. This is the reason why shear sensitive materials like heavily filled resins, fiber-reinforced resins, amorphous resins and gates should be larger according to the injection mold makers in china. This will keep the lower the rise in pressure and temperature.
When you choose the china fundamental of plastic mold design or the oem/odm medical injection mold factory, you should keep in mind the size factor. This will make sure that you end up with a high precision plastic making mould china that can be effective in the prototype production.
Resource box: This article is originally posted in https://www.injectionmouldchina.com.